材質(zhì)復(fù)合橡膠加工工藝塑料 餾化加工方式模壓 沖孔安裝方式按需定制孔型多款
橡膠篩網(wǎng)原材料的塑煉 生膠富有彈性,缺乏加工時(shí)必需的可塑性性能,因此不便于加工。為了提高其可塑性,所以要對生膠進(jìn)行塑煉;這樣,在混煉時(shí)配合劑就容易均勻分散在生膠中;同時(shí),在壓延、成型過程中也有助于提高膠料的滲透性〔滲入纖維織品內(nèi)和成型流動性。 將生膠的長鏈分子降解,形成可塑性的過程叫做塑煉。 生膠塑煉的方法有機(jī)械塑煉和熱塑煉兩種。機(jī)械塑煉是在不太高的溫度下,通過塑煉機(jī)的機(jī)械擠壓和摩擦力的作用,使長鏈橡膠分子降解變短,由高彈性狀態(tài)轉(zhuǎn)變?yōu)榭伤軤顟B(tài)。熱塑煉是向生膠中通入灼熱的壓縮空氣,在熱和氧的作用下,使長鏈分子降解變短,從而獲得可塑性。
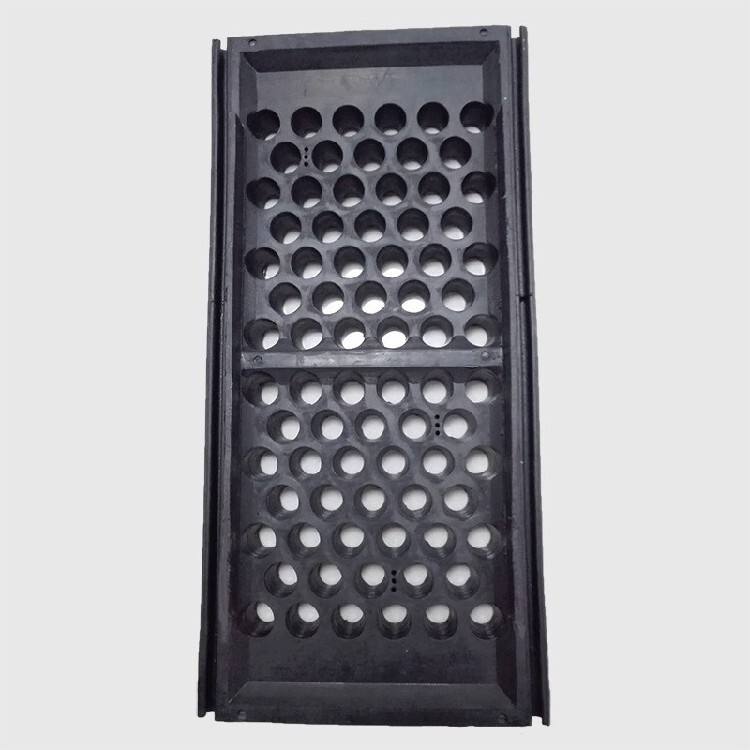
橡膠篩網(wǎng)的質(zhì)檢 1.外觀檢驗(yàn) 篩板表面應(yīng)整潔,無飛過,毛剌等,且不允許有雜質(zhì),無明顯劃痕,泡狀突起.表面紋路自然,表面無可見的微粒,無折射缺陷及澆注口印跡,流痕等. 目測和手感 2.尺寸檢查 橡膠篩板尺寸按規(guī)定程序批準(zhǔn)的產(chǎn)品設(shè)計(jì)圖紙和各相關(guān)的GB標(biāo)準(zhǔn)制造,符合產(chǎn)品圖樣或技術(shù)文件的要求. 卷尺和卡尺 3.耐燃油性檢查 樣品在40OC的環(huán)境溫度下,放在燃油中浸泡48h后,其本積變化率應(yīng)小于10%,硬度變化為-25RHD以內(nèi),拉斷強(qiáng)度變化率應(yīng)在-35%以內(nèi),拉伸變化率在-20%以內(nèi)。
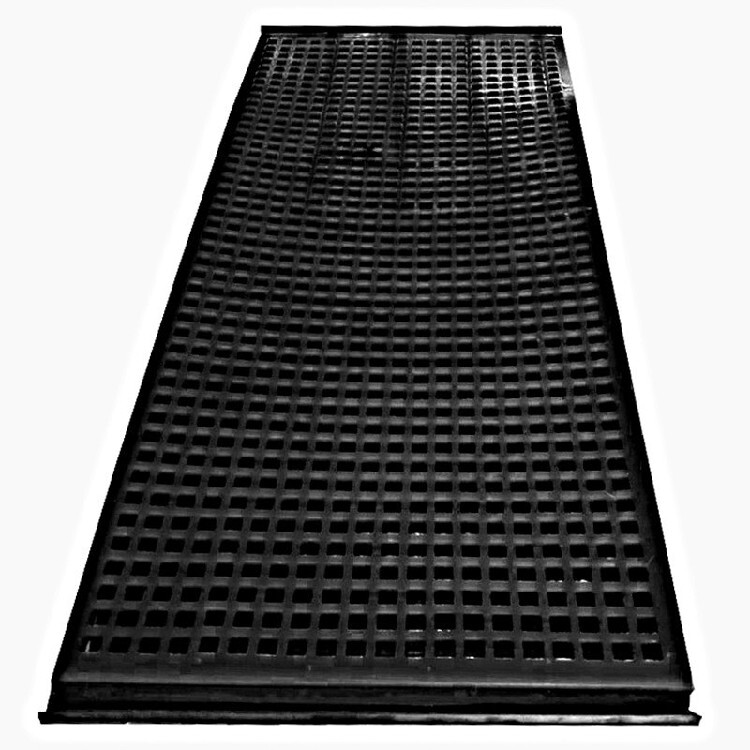
橡膠篩網(wǎng)的質(zhì)檢(二) 4.耐潤滑油性檢查 樣品在70OC的環(huán)境溫度下,放在潤滑油中浸泡72h后,其體積變化率在-10%~+15%之間,硬度變化為-5~+10RHD之間,拉斷強(qiáng)度變化率應(yīng)在10%以內(nèi),伸長變化率在-30%以內(nèi)。 5.硬度檢查 篩板硬度應(yīng)符合產(chǎn)品圖紙或技術(shù)文件的要求。常用橡膠件的材質(zhì)及硬度值,僅作為一般批產(chǎn)件驗(yàn)收參考,如有特殊要求時(shí),請以經(jīng)確認(rèn)的技術(shù)要求執(zhí)行。
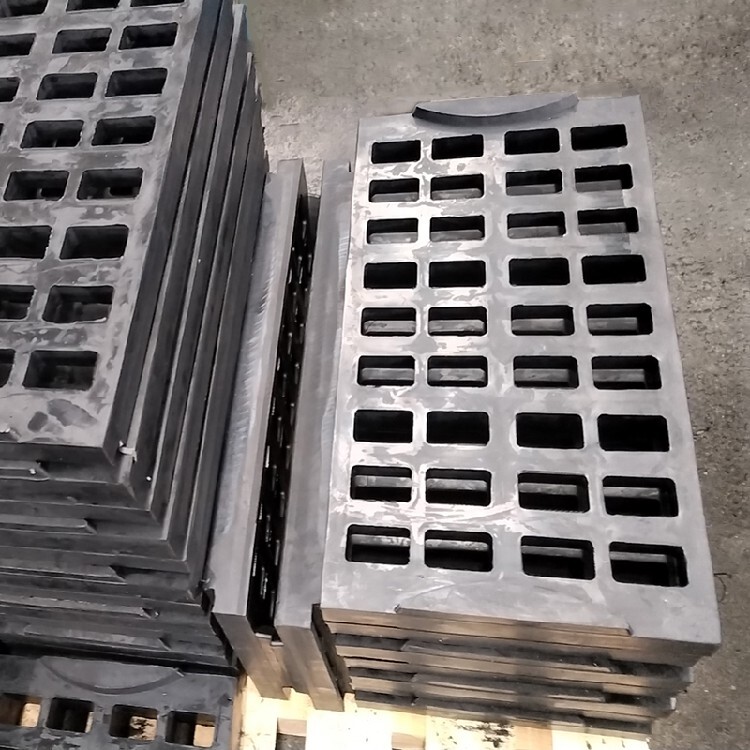
橡膠篩網(wǎng)在加工時(shí),橡膠為何要塑煉 橡膠塑煉目的在于使橡膠在機(jī)械、熱、化學(xué)等作用下切短大分子鏈,使橡膠臨時(shí)失掉其彈性而使可塑性增大,以知足制造過程中的工藝要求。如: 使配合劑易于混入,便于壓延壓出,模壓花紋清楚,形狀穩(wěn)固,增添壓型、注壓膠料的流動性,使膠料易于滲透纖維,并能提升膠料溶介性及粘著性。自然一些低粘度、恒粘度橡膠有時(shí)也不必定塑煉,國產(chǎn)標(biāo)準(zhǔn)顆粒膠,標(biāo)準(zhǔn)馬來西亞橡膠(SMR)。
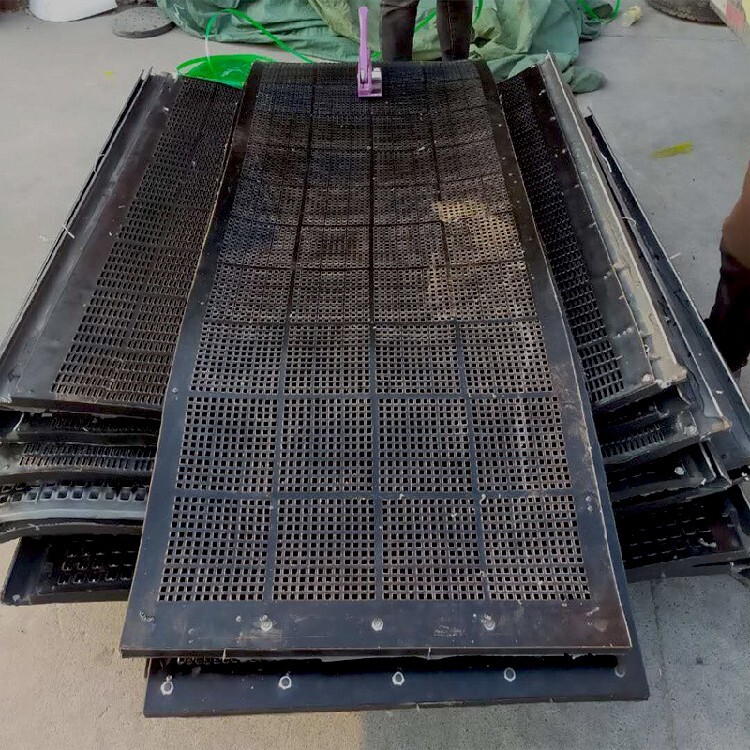
橡膠篩網(wǎng)在生產(chǎn)上,容易出現(xiàn)的問題:脫膠 及解決方案 橡膠-金屬粘接不良 橡膠與金屬的粘結(jié)是橡膠減震產(chǎn)品一個(gè)重要環(huán)節(jié),橡膠與金屬的粘結(jié)原理,普遍認(rèn)為在低模量的橡膠與高模量的金屬之間,膠粘劑成為模量梯度,以減少粘結(jié)件受力時(shí)的應(yīng)力集中。常用雙涂型膠漿的底涂或單涂型膠粘劑與金屬表面之間主要通過吸附作用實(shí)現(xiàn)粘結(jié)。底涂型和面涂型膠粘劑之間,以及膠粘劑與橡膠之間通過相互擴(kuò)散作用和共交聯(lián)作用而實(shí)現(xiàn)粘結(jié)。 橡膠-金屬粘接不良的原因分析及解決方法 1 膠漿選用不對。解決方法:參考具體使用手冊,選擇合適的膠粘劑 2金屬表面處理失敗,以致底涂的物理吸附不能很好的實(shí)現(xiàn)。解決方法;粗化金屬表面,金屬粘結(jié)表面一定的粗糙度。常用的處理方法,顯微鏡觀察表面粗糙度從大到小依次是噴砂、拋丸>磷化>鍍鋅.金屬表面不能有銹蝕,不能粘到油污、灰塵、雜質(zhì)等 3膠漿涂刷工藝穩(wěn)定性差,膠漿太稀、漏涂、少涂、殘留溶劑等。解決方法;注意操作,防止膠漿漏涂、少涂。

橡膠篩網(wǎng)在加工時(shí),容易出現(xiàn)的問題-撕裂、拉毛 及解決方法 撕裂、拉毛表現(xiàn)在橡膠接頭膠體被扯斷或橡膠體表面不光滑平整。撕裂、拉毛的原因和解決的方法如下; 8.1脫模方式不合理,硬脫模,導(dǎo)致制品被扯斷或拉毛。解決方法;改進(jìn)脫模方式,改進(jìn)模具結(jié)構(gòu)。噴脫模劑 8.2制品過度硫化,導(dǎo)致橡膠強(qiáng)度等物理性能下降而被撕裂、扯斷。解決方法;調(diào)整硫化條件到正硫化。 8.3硫化溫度太高。解決方法;調(diào)整膠料配方,降低硫化溫度。